Forged Steel vs. Cast Steel
March 3rd, 2024
5 minute read
Ever wondered what it means when you read about gun parts being “cast” or “forged”? Metal is metal, so it shouldn’t matter, right? Wrong. The quality of the materials and construction of your firearm is of the utmost importance. So, let’s dive into this subject here and see if we can make some sense of it all.
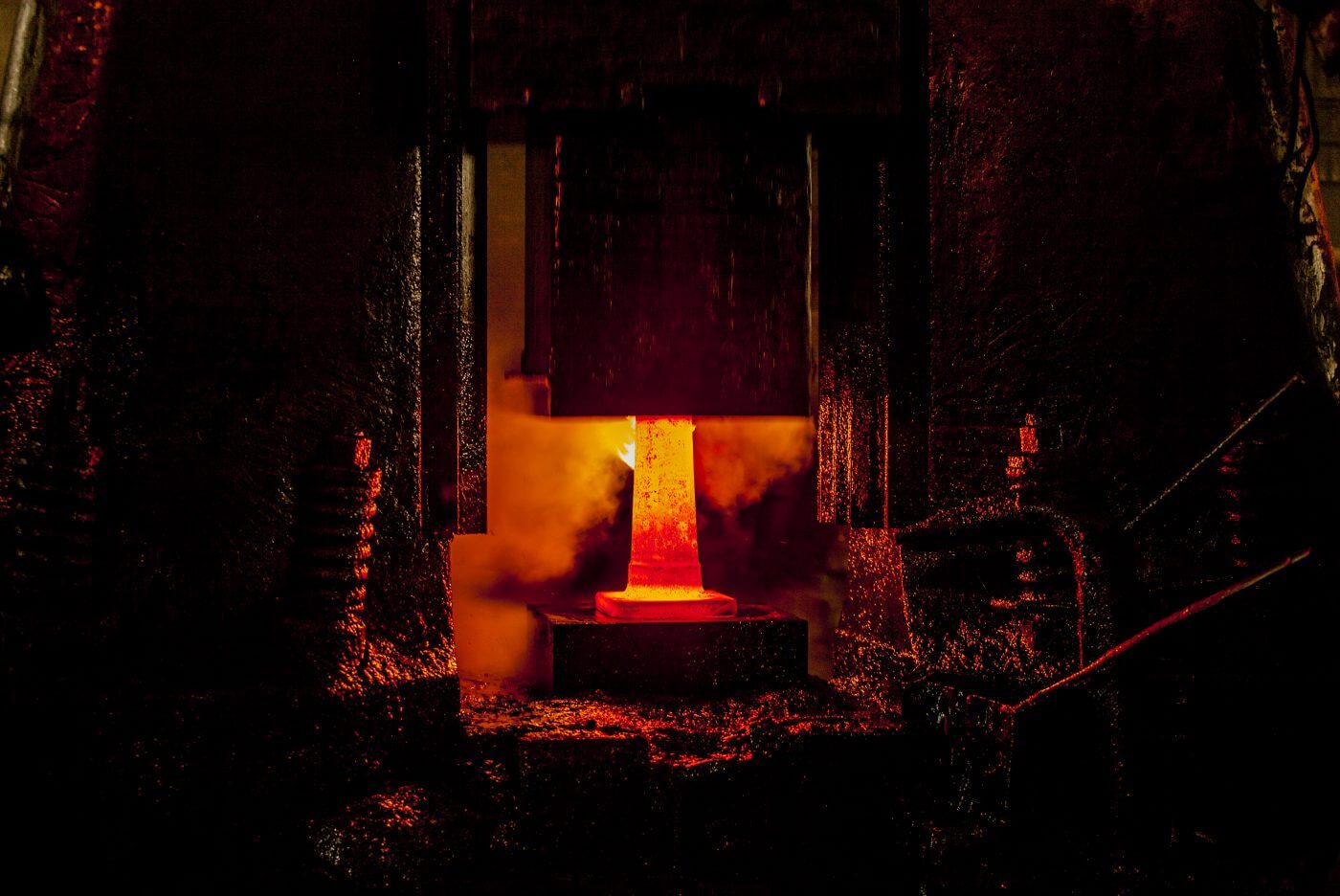
Iron is a most remarkable material. With an atomic number of 26 and an atomic weight of 55.845, iron is extraordinarily versatile stuff. It melts at 2,800° F and boils at 5,182° F. In its elemental state, iron reacts quickly with oxygen and water to form oxides in the form of rust. However, mix that iron with a little special sauce like carbon, chromium, nickel and the like, and you get various steels. That stuff can be used to do some of the most wonderful things. Not least among them is making gun parts.
What Is Steel Casting?
You may have heard of cast versus forged steel, but wondered what the difference was. Steel is not the amorphous homogenous stuff it appears to be on the outside. Steel actually has a complicated internal microcrystalline structure that has been exhaustively studied. This microstructure determines such characteristics as strength, ductility and wear resistance. Optimizing these properties is critical to producing quality gun parts that will last. Frequently, manufacturing processes come down to balancing function and durability against cost.
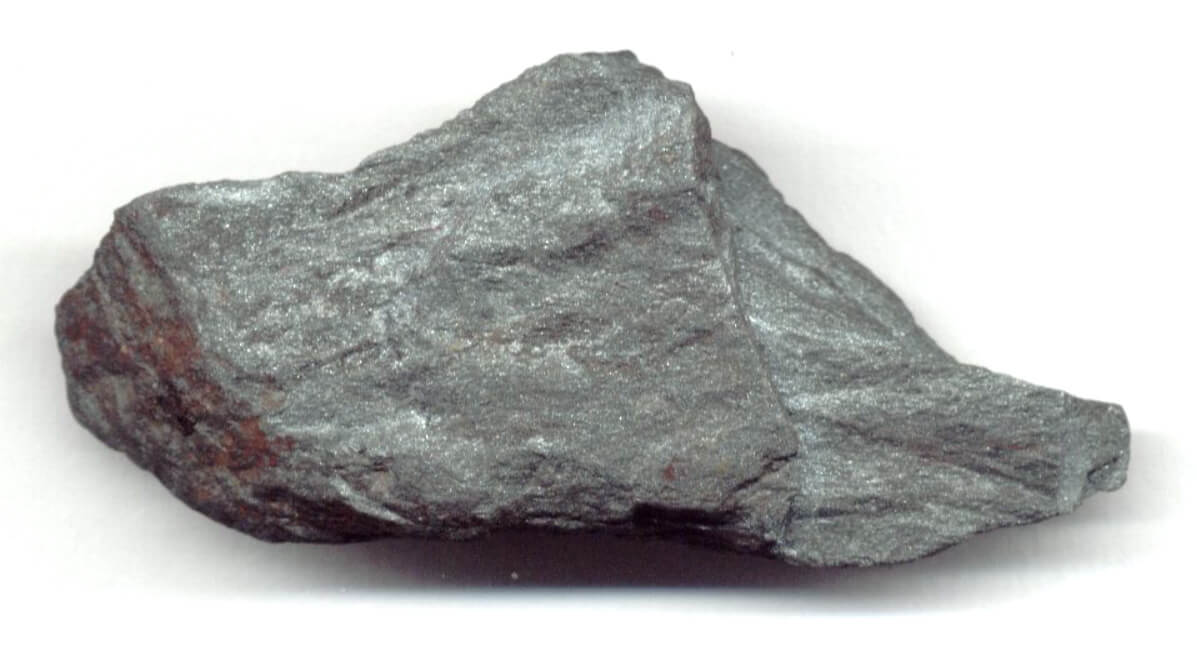
Steel casting involves pouring molten steel into a mold and allowing it to harden as it cools. Casting is amenable to the manufacture of complex shapes and particularly large parts. However, cast parts end up with a random crystalline microstructure that makes them potentially weaker than forgings. Castings can also include microscopic porosities from little gas bubbles or other impurities retained within the metallic structure that can cause potential weak spots.
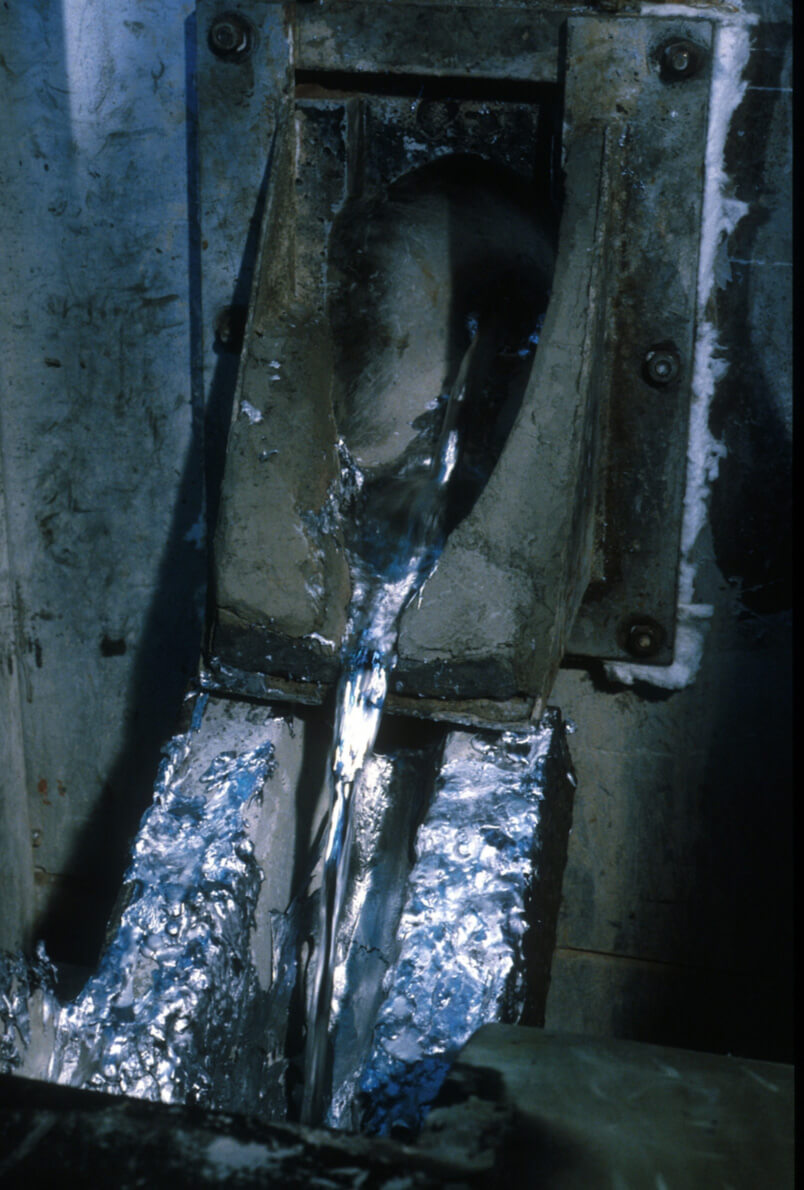
Investment casting dates back at least 5,000 years and involves using some type of solid 3-D pattern made from something like wax within a ceramic mold. Filling the mold with molten steel vaporizes and displaces the filler. So long as care is exercised, cast parts can be produced in quantity and require minimal surface finishing. However, forgings will have more potential strength.
Is the Forging Process a Better Option?
Forging involves the application of thermal and mechanical energy to steel billets causing the material to change shape while remaining in the solid state. Advantages to forgings include retention of uniformity of composition and crystalline structure within the material. The thermal cycle and organized deformation associated with the forging process result in grain refinement and controlled metallurgical recrystallization. As a result, forgings are generally stronger and tougher than castings or plate steels as the critical internal grain flows of the material conform to the shape of the part.
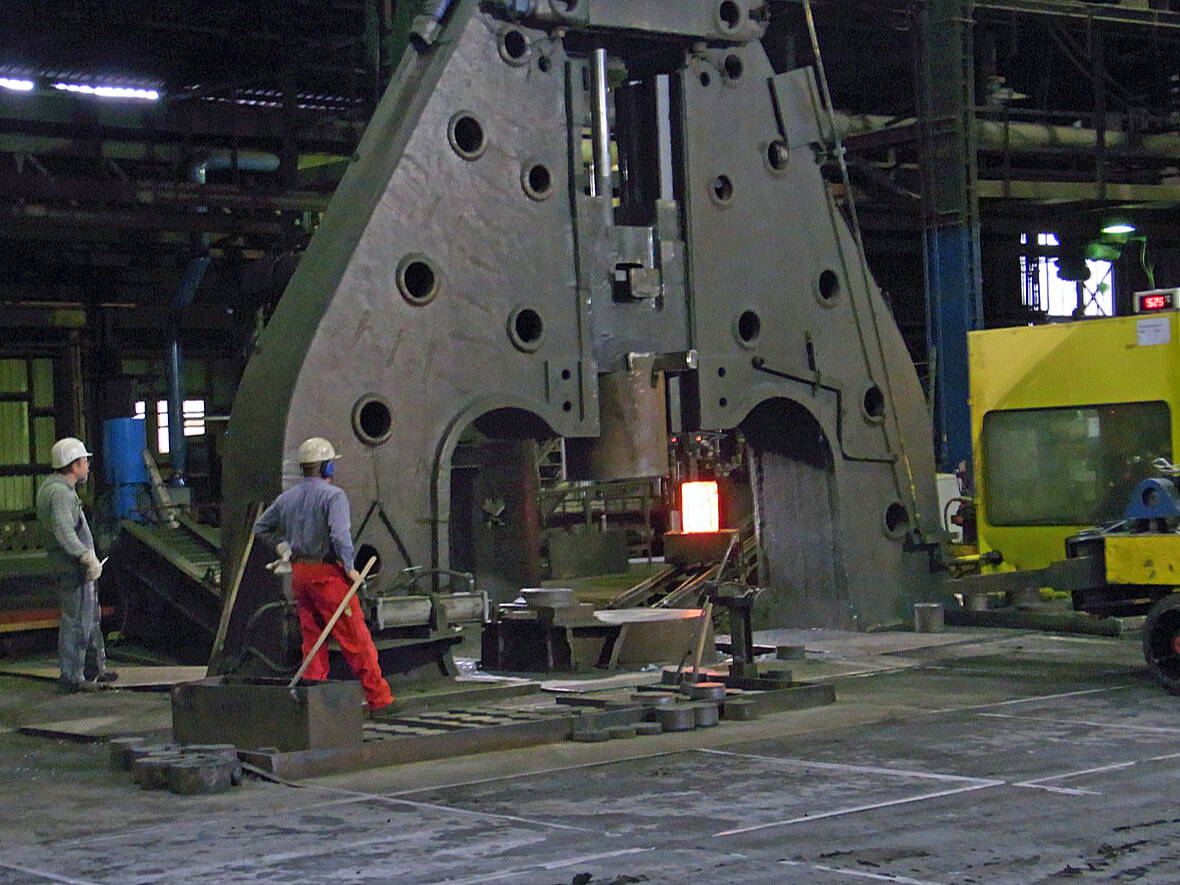
Sound complicated? Yes. But the point is much more simple. The result of forging is a piece of steel without internal irregularities or weak points. That means your forged part will be stronger and more durable.
Forging or Casting: What Difference Does It Make?
Honestly, if you are making barbecue grills or floor lamp components, this added strength may not matter a whole lot. Cast parts are plenty strong and plenty tough to keep your doorknobs and coat hooks going until the sun burns out. For more critical stuff, however, the differences become more significant.
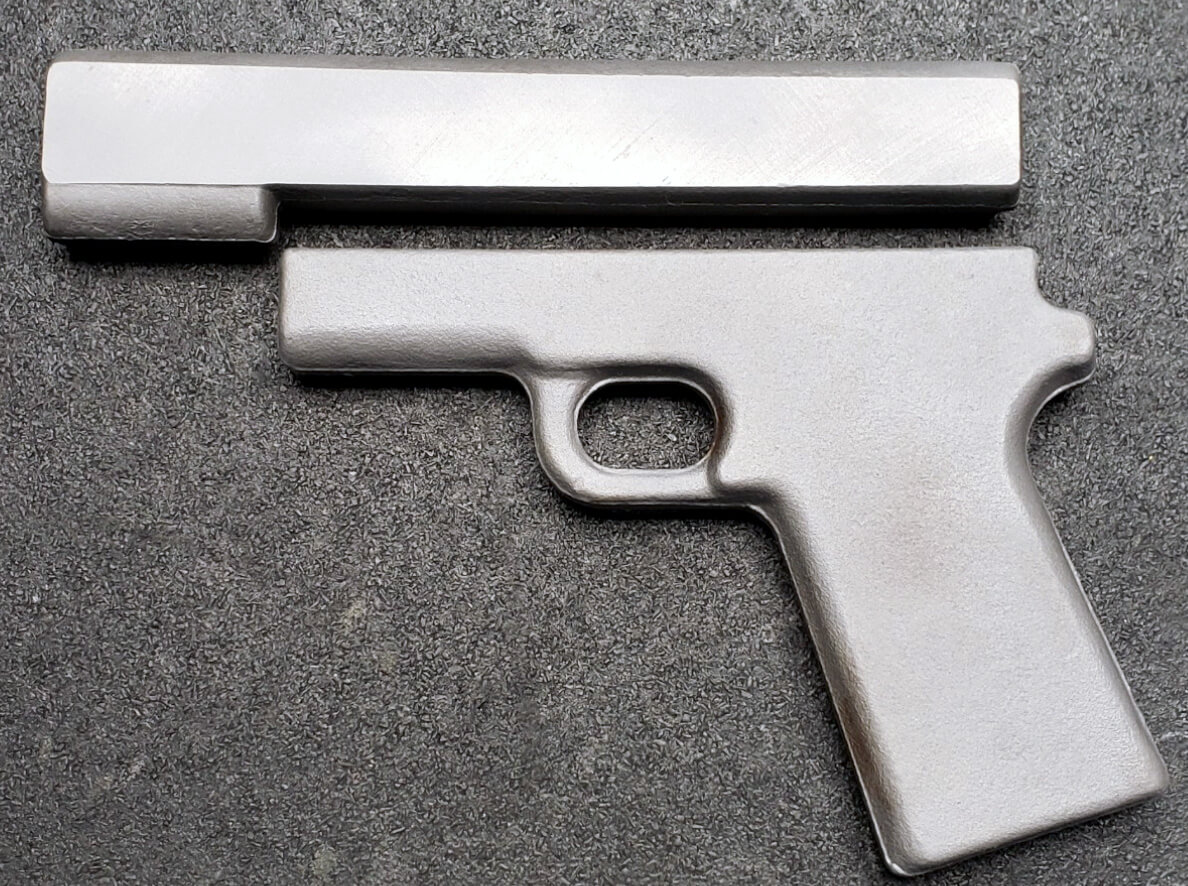
For parts that are expected to withstand repeated heating cycles and extended mechanical trauma, forged components wear better and resist failure longer than their cast counterparts. Cast parts are frequently more affordable, but forgings will always be heartier. For a handgun frame, for instance, forged components are better suited to high round counts and hard long-term use.
The Source
So, it would make sense that firearms made with forged components like slides, barrels and frames would be stronger, right? As a result, Springfield Armory uses forged components exclusively for a majority of their firearms components. From the Ronin to the Hellcat, critical parts including slides and barrels are made from top quality steel forgings. This results in a firearm you can count on despite egregious operational abuse and still expect to hand down to your grandchildren’s children.
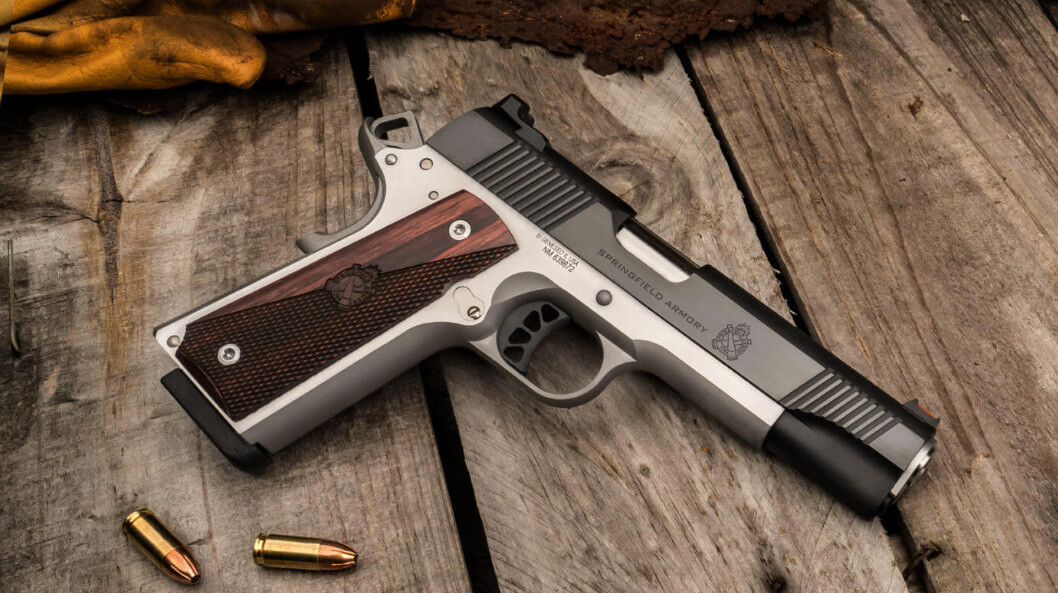
Using the 1911 Ronin as an example, the slide is made from forged carbon steel. The barrel and frame are machined from forged stainless. These critical components are then precision machined to their final shape while retaining the precise microstructural properties necessary to maximize wear resistance and toughness. The end result is a remarkably durable and long-lasting 1911 handgun.
Oh, and remember how I mentioned forged parts are generally more expensive than cast ones? Well, thanks to Springfield Armory’s expertise in manufacturing, they can offer forged components in many guns with very reasonable price points. Remember that Ronin I was mentioning? Like all Springfield 1911s, it has a forged frame and slide. But, it also has an MSRP of just $917. You’d be hard-pressed to find a gun with comparable features and even cast parts for that price. So, you get more for less. Pretty good deal, right?
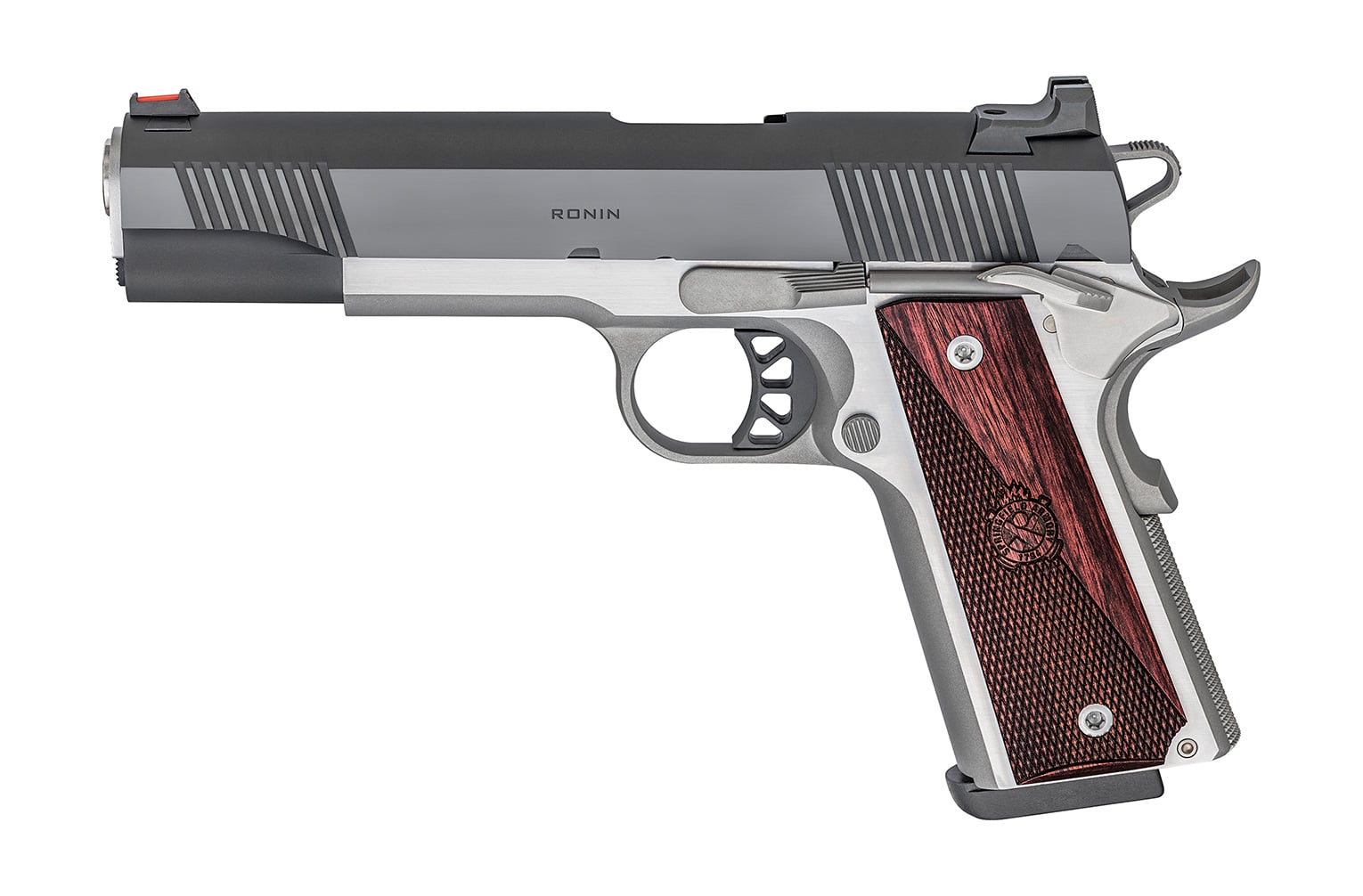
[Be sure to read Paul Carlson’s article on the Springfield Ronin 10mm.]
What to Consider When Choosing Between Them?
In many cases, a cast part may be just fine. But, if you can get something made with a potentially stronger part and not have to pay a premium for it, why not? This is particularly true when it comes to defensive firearms.
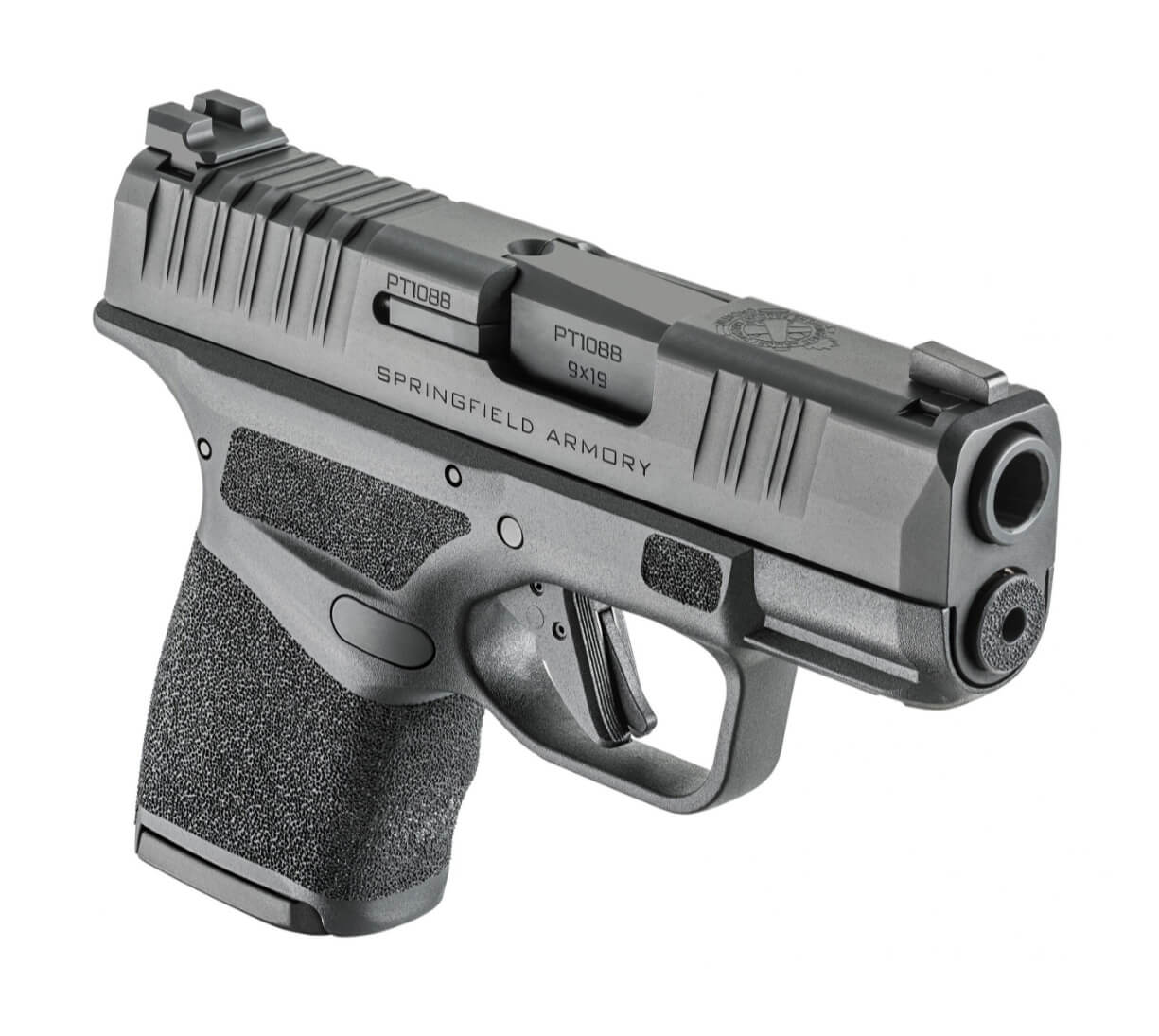
Choosing a defensive firearm can be one of the most important decisions a person will make. Should you ever have to use that gun for real it will suddenly become more valuable than your house and your 401k, combined.
Editor’s Note: Be sure to check out The Armory Life Forum, where you can comment about our daily articles, as well as just talk guns and gear. Click the “Go To Forum Thread” link below to jump in!