Big Green Is Back: The Story Behind Remington Ammo
October 2nd, 2021
5 minute read
Ever wonder what it takes to make ammunition on a massive, commercial scale? I’ll admit that I had never really thought about it. I, like everyone else, just go to the store and buy ammo and never think about what goes into the manufacturing process behind it.
I recently had a chance to find out for myself exactly how much is involved when I got to visit the “Big Green Mini-City” that is Remington’s Lonoke, Arkansas ammunition facility. Whether it be 9mm target rounds or 12-gauge buckshot, if it says Remington on the package it comes from here. The facility, as well as the employees that work there, have gone through a lot in recent years, but they are making a very strong comeback in 2021.
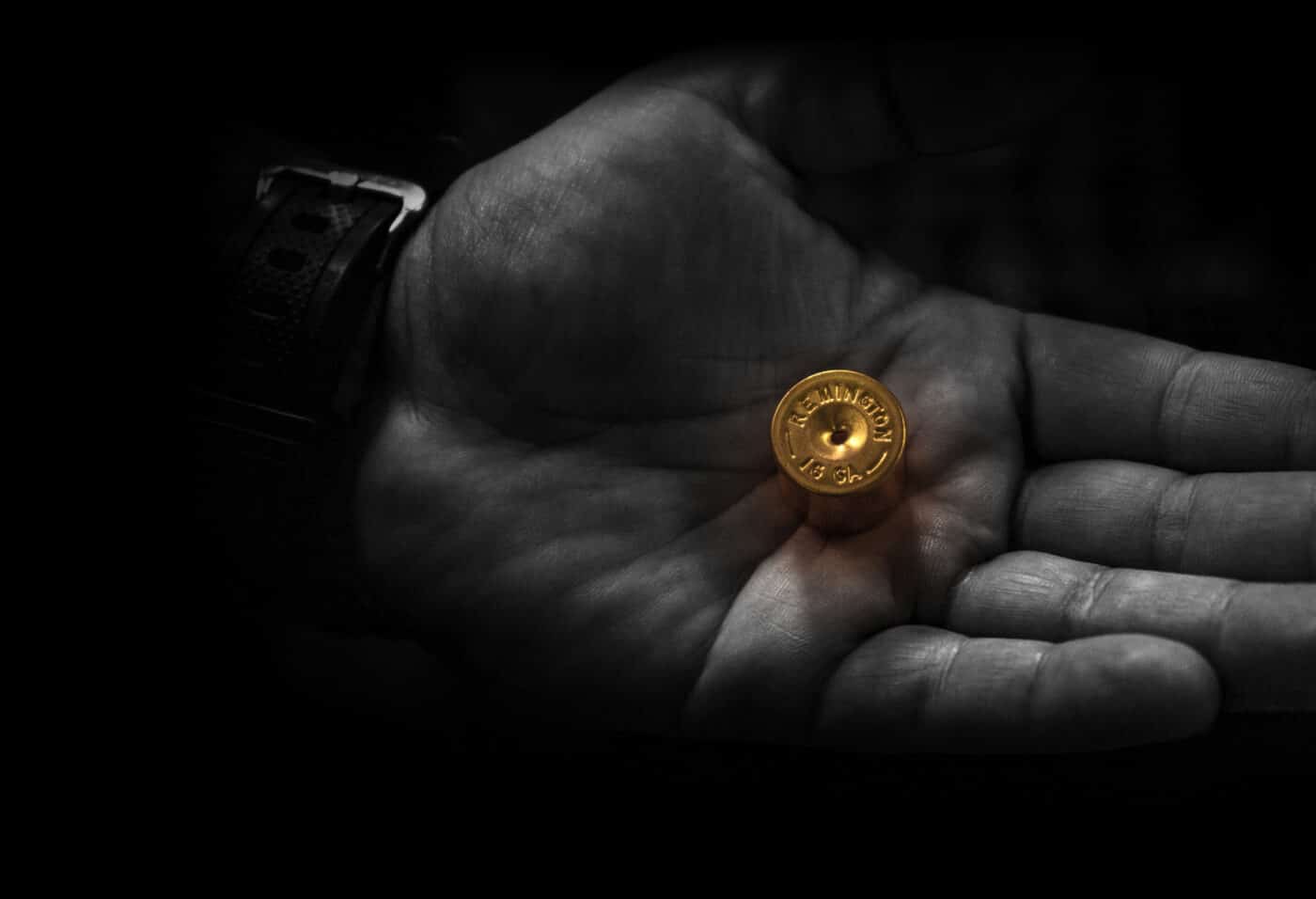
Moving Forward
Remington Ammunition was purchased out of bankruptcy last fall. Since that time, the company has hired hundreds of workers, increased output significantly and continues to grow and expand. There is no secret of how high the demand for ammunition is across the country these days, and it was interesting to see Remington making so much of it in so many different calibers. From bulk 9mm to non-toxic waterfowl loads, the factory was abuzz with activity, resulting in countless boxes and cases going out the door each day.
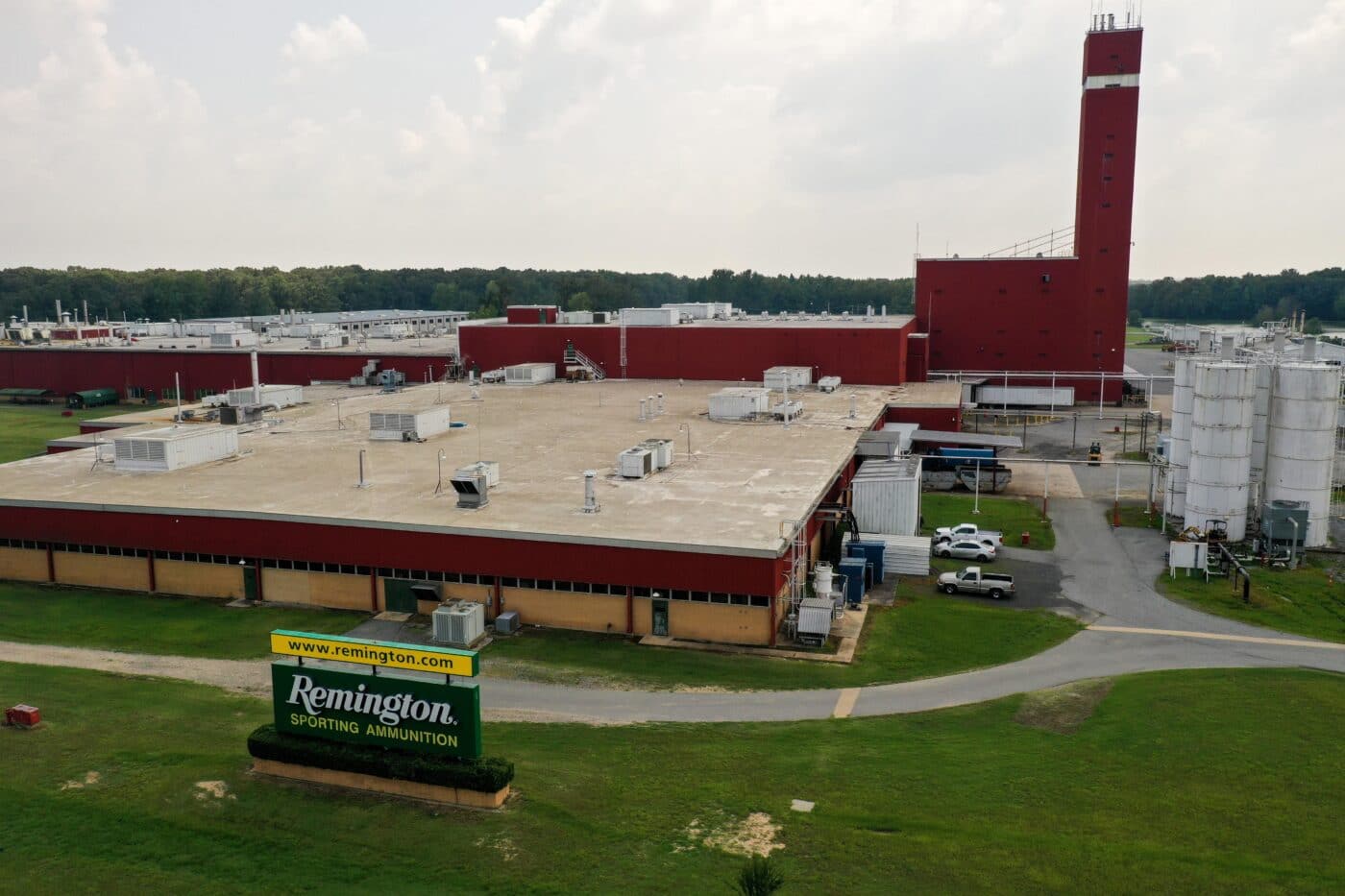
Located 20 miles from Little Rock, Arkansas right off I-40, the massive facility is situated on 1,200 acres of land. There’s more than 800,000 square feet of manufacturing and warehouse space in the facility — and that too has recently increased. We even got a chance to see a new wing of the factory that featured modernized machinery and processes, all working together to help get ammo out the door. To say the state-of-the-art manufacturing capabilities at the plant were impressive would be an understatement. Also, the mountains of raw materials that are turned into ammunition are just incredible to see.
The last few years had been tough on the factory, the employees and the community, but the acquisition by Anoka, Minnesota’s Vista Outdoor ensured that the famous “Big Green” maker of the iconic green boxes of ammo was back — and in a big way. An unstinting effort was made to retool the plant in early 2021, ramping up production and running 24 hours a day, seven days a week, to keep store shelves stocked with its in-demand products.
A Towering Role
While its capacity to produce rifle and pistol ammunition is amazing, the Big Green facility is also known for its production of shot for shotshells, coming from the famous “Shot Tower.” Let me tell you, having seen it in person, it’s stunning and truly impressive. The Shot Tower’s optimal height is a full 11 stories tall.
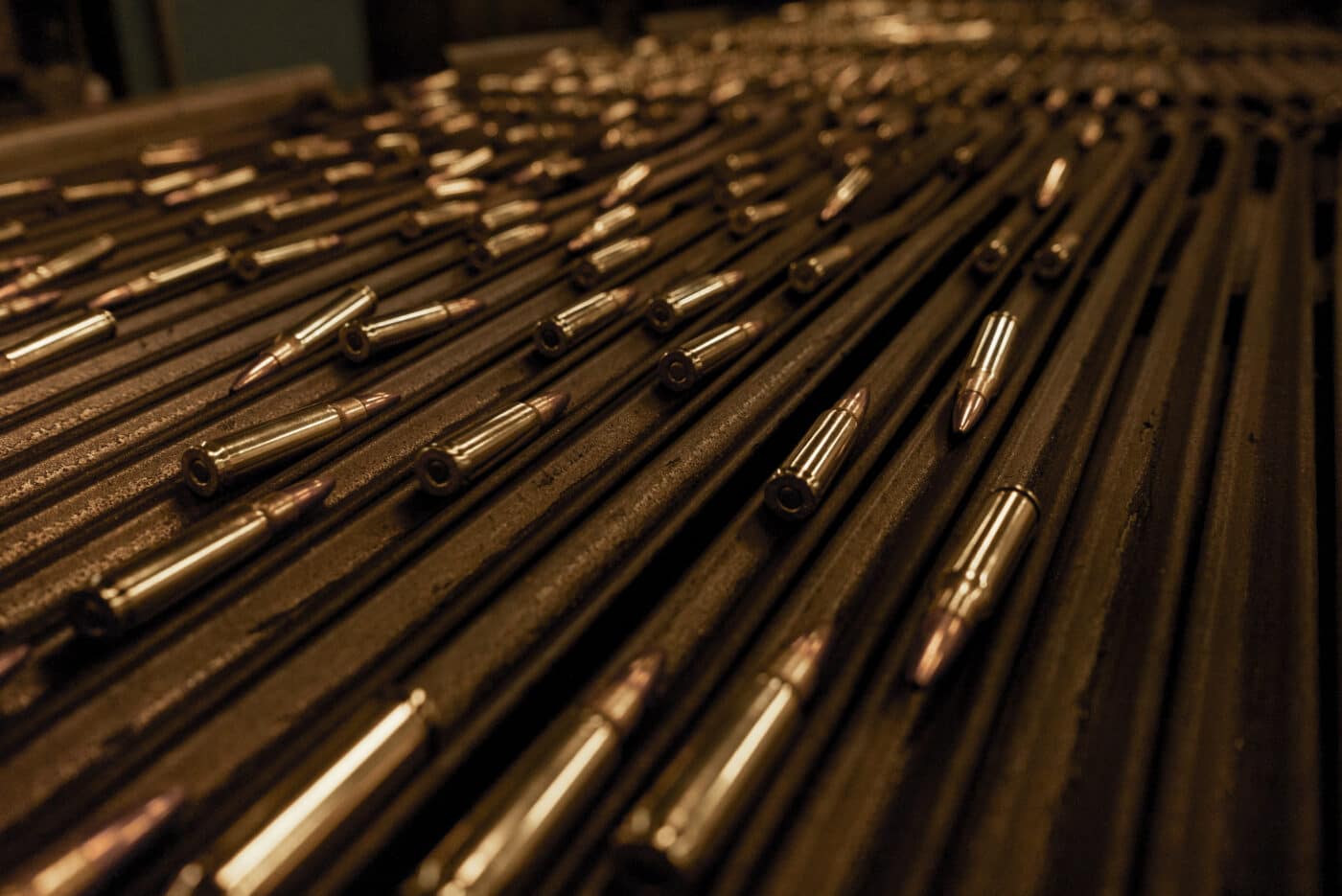
You access the tower from an original freight elevator that takes you up to the top. Here, a very large kiln holding tank of molten lead is housed. A pipe from the kiln runs to a tray, allowing molten lead to run out and through a specific-sized screen for the size shot being produced. The lead shot then free falls the 11 stories down into a holding tank of water, which quickly finishes the cooling of the shot. Lead naturally becomes a sphere as it falls and cools for the drop.
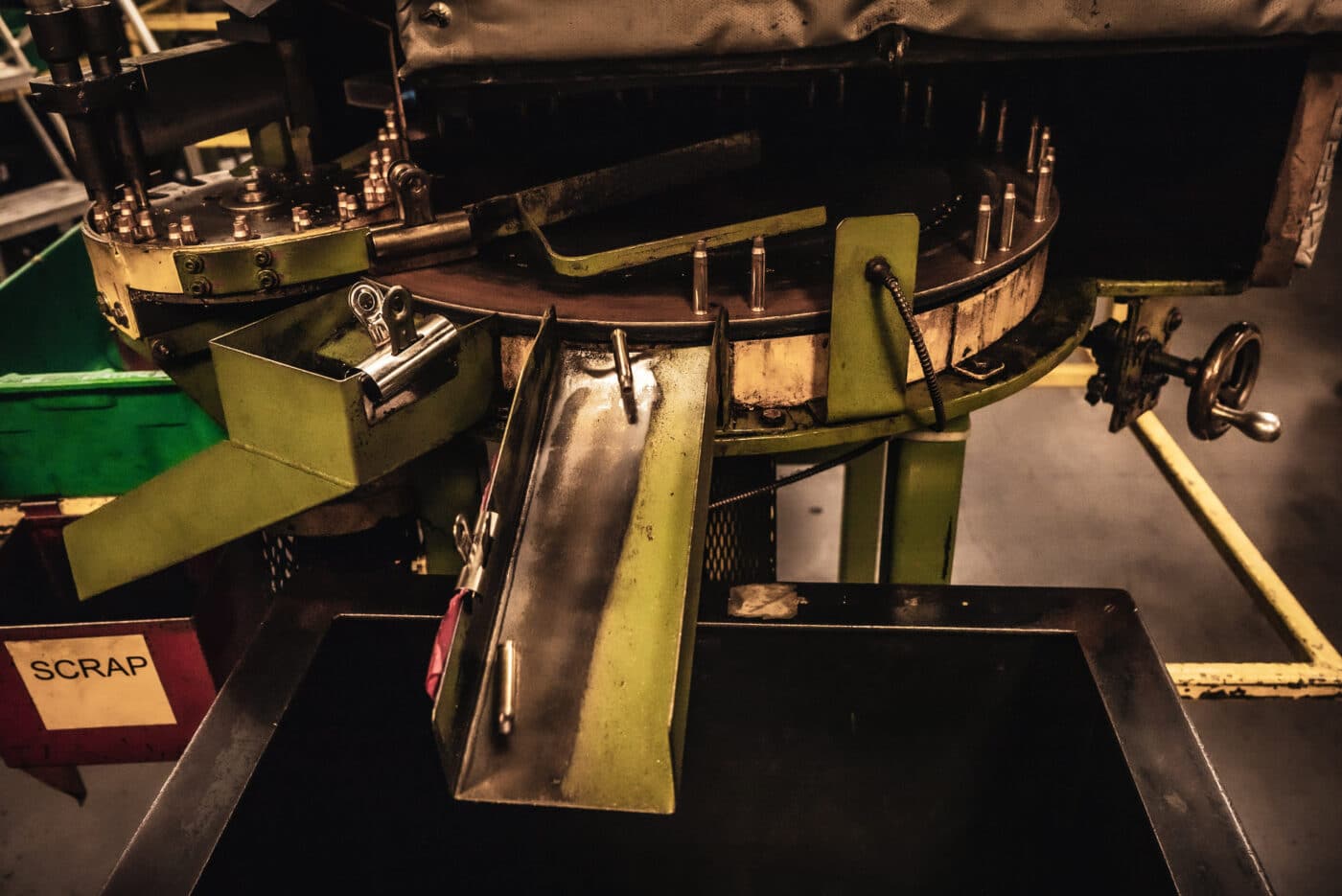
The next step for the lead shot is a series of glass tables the shot runs down. This method is used to separate out odd sizes and defective pieces. The shot then travels into a series of tumblers that sort the lead shot into thick steel holding containers in the floor. Below these containers is another floor where workers dispense the amount of shot needed for loading shells.
Remington makes every single component of their shotgun shells at the facility. Shotgun shell hulls start as small pellets of clear plastic mixed with whatever color pellets the shell will be. It’s melted and extracted out of the machine in a giant roll of plastic that looks a lot like PEX pipe (if you are familiar with plumbing). This pipe is cut into small piece of plastic that later will be stretched and thinned out to make six long plastic tubes thinned and sized for processing. These six pipes are approximately two-feet long before they are cut to length, as well as having grooves added to make the shell easier to handle when loading into your shotgun.
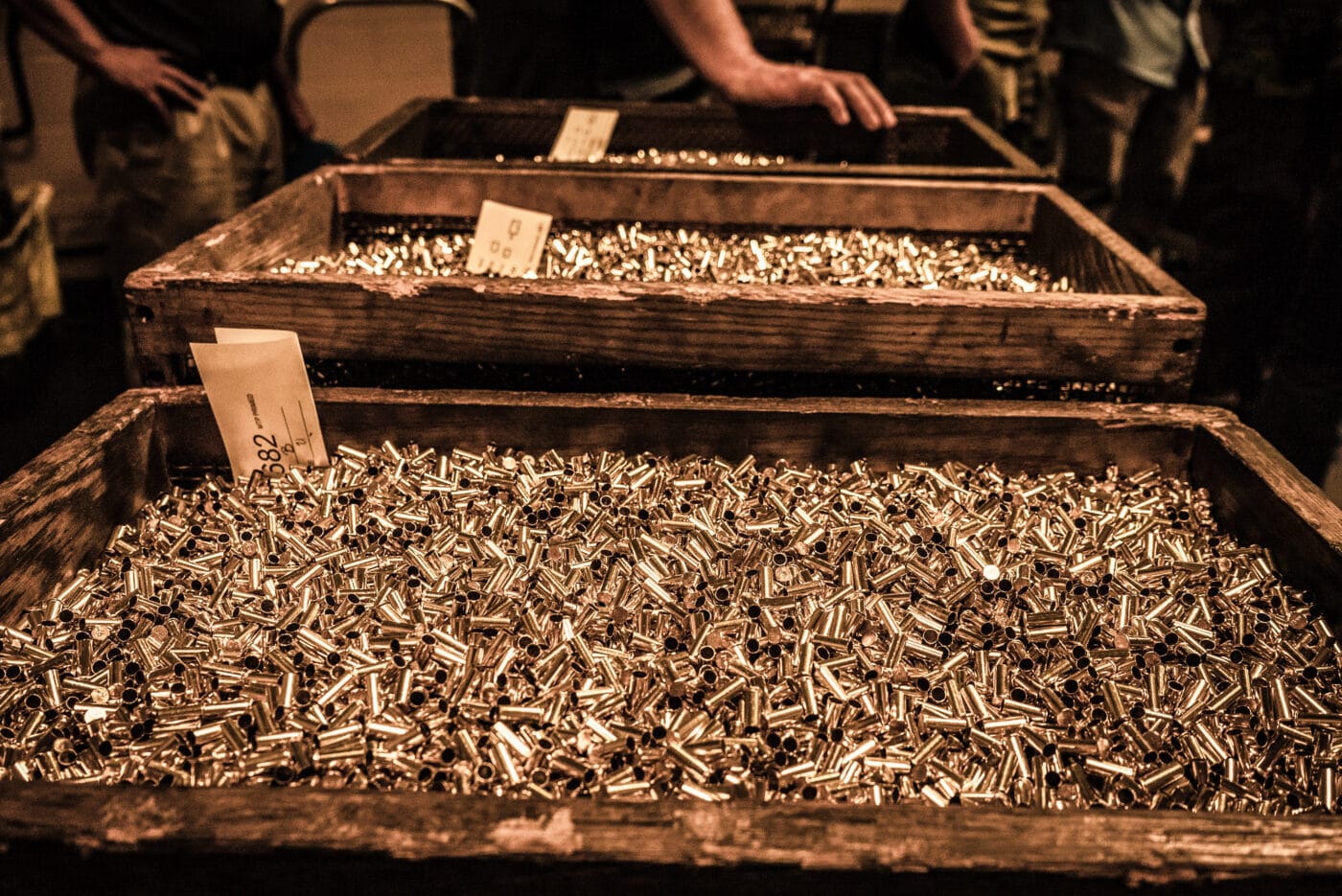
Rimfire ammunition is also produced at the facility. Millions of rounds a year come out of the rimfire machines. There are only a handful of facilities here in the United States that can manufacture rimfire ammunition, so the Lonoke Remington plant is clearly a major player in this market.
Conclusion
Remington’s state-of-the-art Lonoke Arkansas Big Green facility is back, and it is clearly here to stay. Having seen it myself, I can honestly say both the facility and the processes it uses to produce ammunition and components are incredible. With ammo so hard to find these days, we need an important brand like this doing its part to supply this need. I could not be more happy to see that the Big Green is back!
Editor’s Note: Please be sure to check out The Armory Life Forum, where you can comment about our daily articles, as well as just talk guns and gear. Click the “Go To Forum Thread” link below to jump in and discuss this article and much more!